Preheater
The performance of the preheater and calciner is an important factor influencing the heat consumption of modern kilns. The IKN Low Under-Pressure Cyclone (LUCY) preheater provides the desired heat exchange between gas and raw meal while keeping the pressure drop low.
Key components such as cyclone inlet spiral and the arrangement of the riser ducts have been developed and refined to achieve the best overall performance. The design avoids unwanted areas of turbulences to minimize or even eliminate buildups. The design concept is flexible and adaptable to be incorporated into existing preheaters.
The main features of the LUCY Preheater are:
- Effective meal dispersion into the gas stream by the design and location of splash boxes.
- Excellent heat exchange between raw material and gas.
- Efficient separation of raw meal at each cyclone stage with low pressure drop.
- Comparatively low height and reduced footprint.
IKN’s proprietary process expert system provides the theoretical foundation for the design of each LUCY Preheater. Local specifications further influence the final layout.
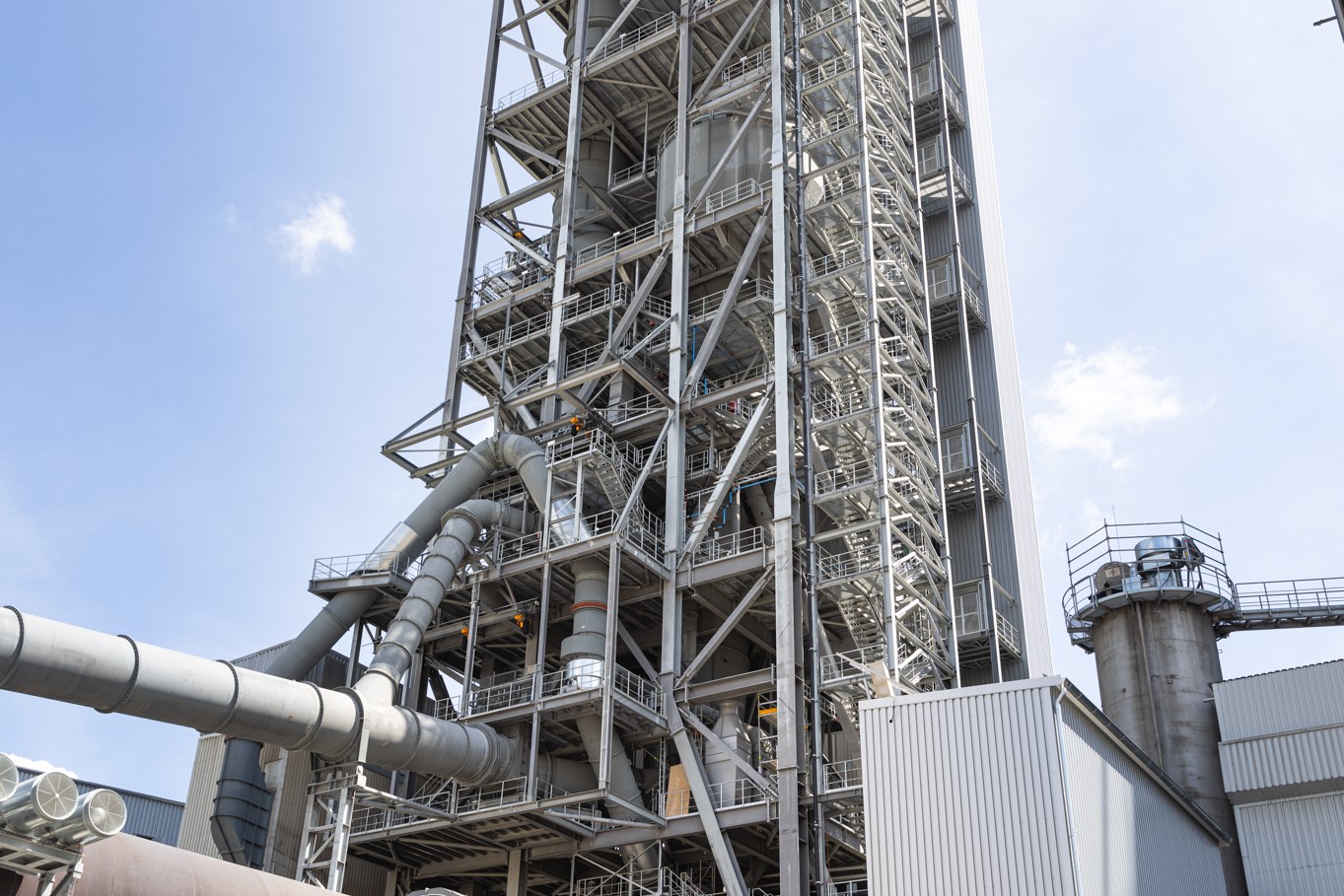
Cyclone Design
Key elements of the LUCY Preheater are cyclones with low pressure loss. Top stage cyclones are designed for maximum dedusting efficiency.
The number of cyclone stages determines the specific fuel consumption. It is a compromise between the efficiency of the preheater and drying requirements of the raw meal.

Calciner Technology
Modern Calciner technology faces many operational challenges such as high AF usage and strict emission limits.
Calcination rates of 90% and more are achieved with approximately 60% of the total fuel directed to the calciner. As the combustion of fuel and the calcination of raw material take place outside of the rotary kiln, the heat loading of the kiln is reduced and smaller rotary kilns are possible.
All IKN calciners are based on a modular system. Calciner solutions are designed by experts according to the fuel used, available space and other specific requirements.
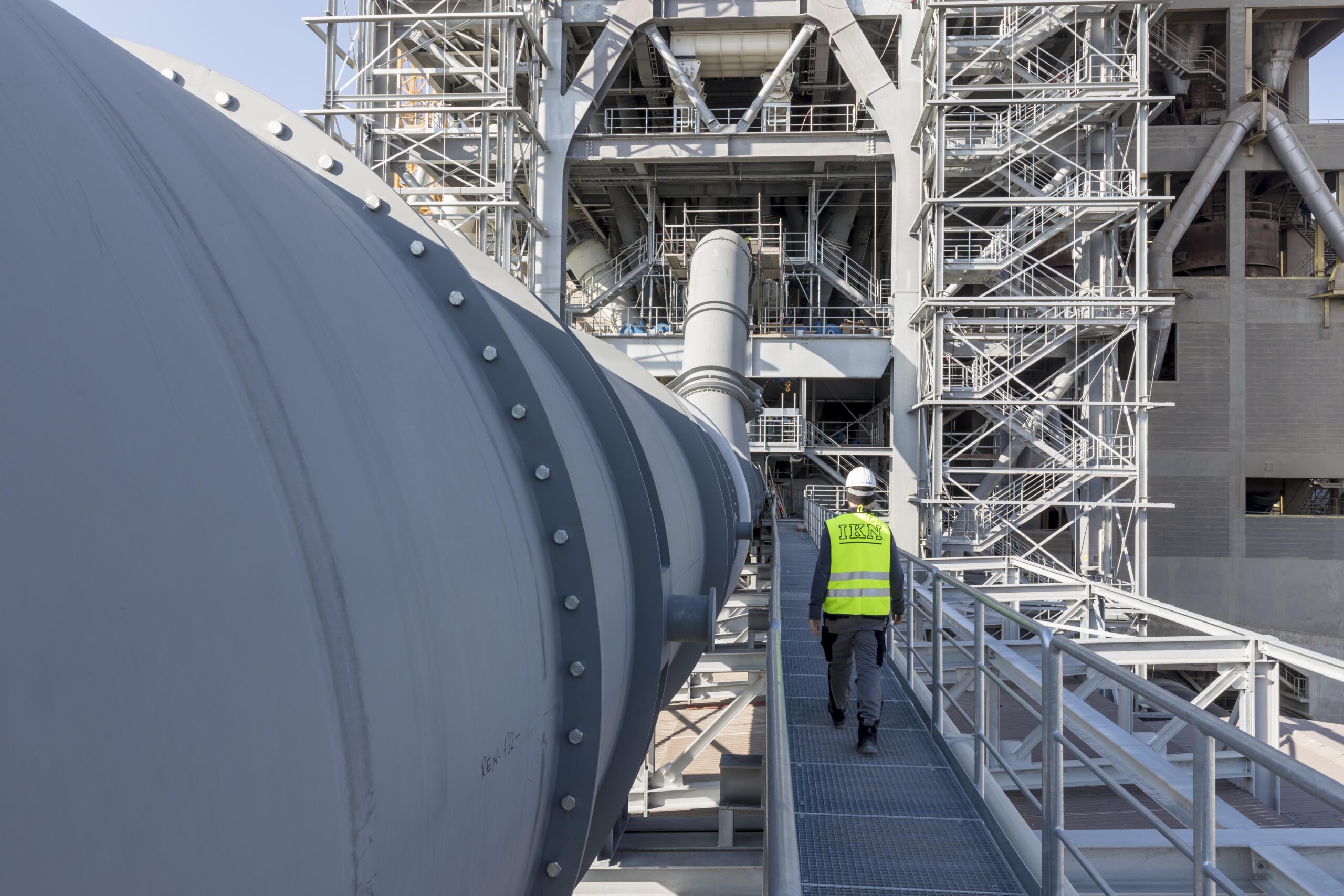
In the IKN Calciner, raw meal feed points provide additional means to control and maintain proper temperature. Heterogenous alternative fuels that are coarse and of low quality are fed into the calciner through the IKN Fire Bed Combustor (FBC). The FBC reactor connects the alternative fuel feeding system to the calciner. During the transition through the reactor, flyable fuel particles are separated while the residence time of non-flyable particles is extended before they eventually discharge into the calciner.
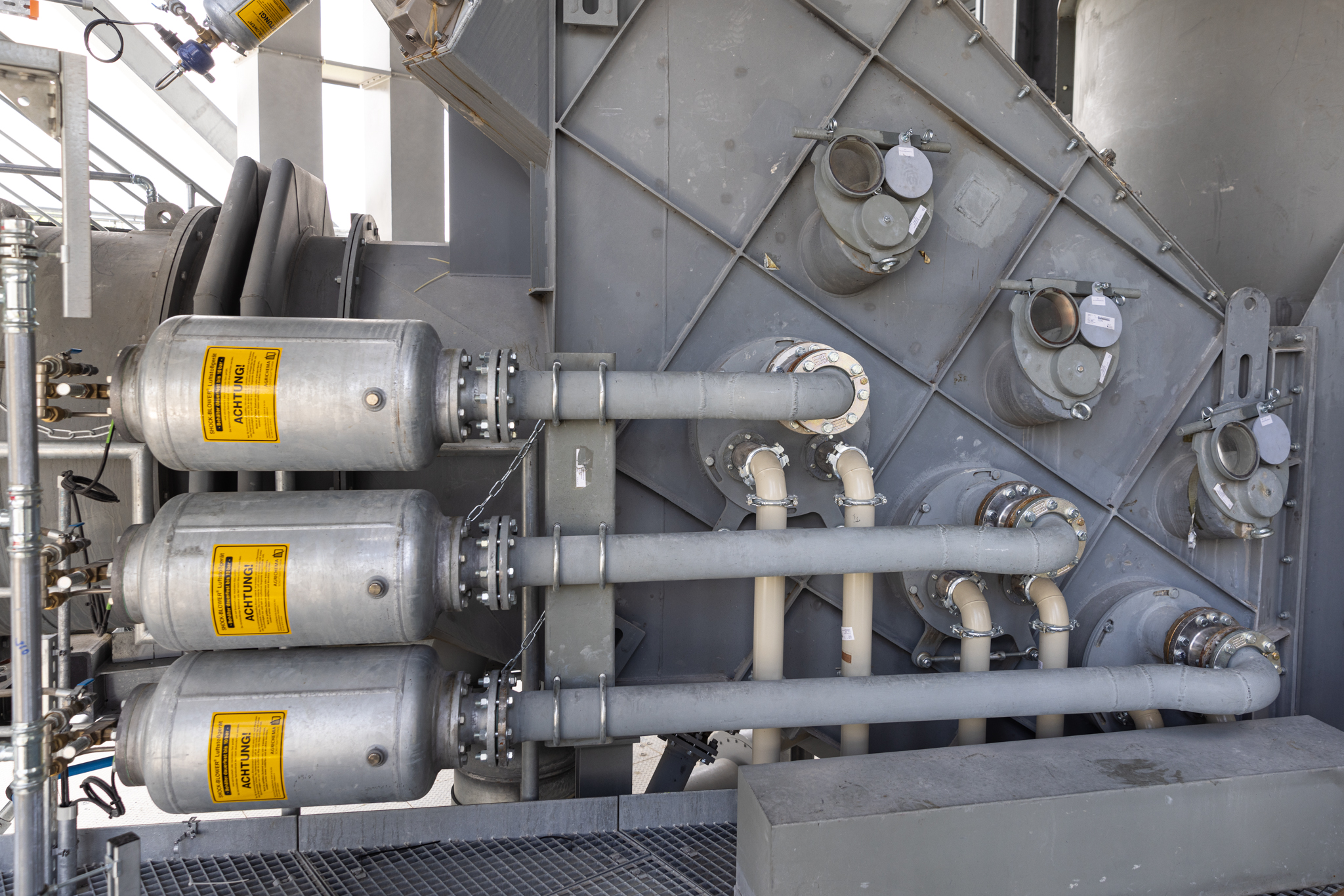